In the manufacturing of metal wire products, annealing is more than just a heat treatment process—it's a critical step that defines the final mechanical and electrical performance of the material. A well-engineered Wire Annealing Machine plays a vital role in achieving this outcome by precisely controlling temperature, atmosphere, and line speed. The purpose of annealing is to alter the internal structure of the wire, reducing hardness, relieving internal stresses, and improving ductility. These changes are essential in making the wire suitable for drawing, coiling, or final application in demanding sectors such as automotive, construction, and electronics.
At the microscopic level, wire annealing influences the grain structure of the metal. Cold-drawn wire tends to have elongated, distorted grains that are hard and brittle. When passed through an annealing machine at controlled high temperatures, these grains recrystallize into a more uniform and equiaxed structure. This transformation significantly improves the wire's malleability and elongation, which are key properties for further processing. Especially in high-precision applications like electrical wiring or fine spring wire, consistent grain size and improved microstructure are non-negotiable quality indicators.
Equally important is the impact of annealing on electrical conductivity, particularly in copper and aluminum wires. Cold working increases dislocation density in the metal lattice, which hampers the free flow of electrons. A wire annealing system alleviates this by allowing atomic reorganization and reducing structural defects, resulting in lower electrical resistance. For industries that depend on low-loss energy transmission or high-speed signal flow, such as telecommunications and power distribution, the role of annealing becomes a determining factor for performance.
The selection of an annealing method—whether through resistance heating or furnace-based systems—also affects the metallurgical outcome. A high-quality Wire Annealing Machine must offer uniform temperature distribution and a stable processing atmosphere. Inadequate heating can leave residual stresses, while overheating can coarsen grains and degrade surface finish. It's this fine balance between heating rate, dwell time, and cooling speed that defines a machine's effectiveness. Manufacturers with long-term process experience understand how to customize these parameters to match specific material compositions and production requirements.
Controlling the atmosphere during annealing is another vital aspect. Oxidation during the process can cause discoloration, poor adhesion for coatings, and reduced conductivity. That’s why advanced annealing machines often incorporate inert gas systems, such as nitrogen or argon purging, to maintain surface integrity. Especially for wires destined for high-end industrial use, a clean, oxide-free surface is not just aesthetic—it’s a performance necessity. Customers increasingly demand not only functionality but also traceable process quality, and this is where a well-designed wire annealer can truly deliver.
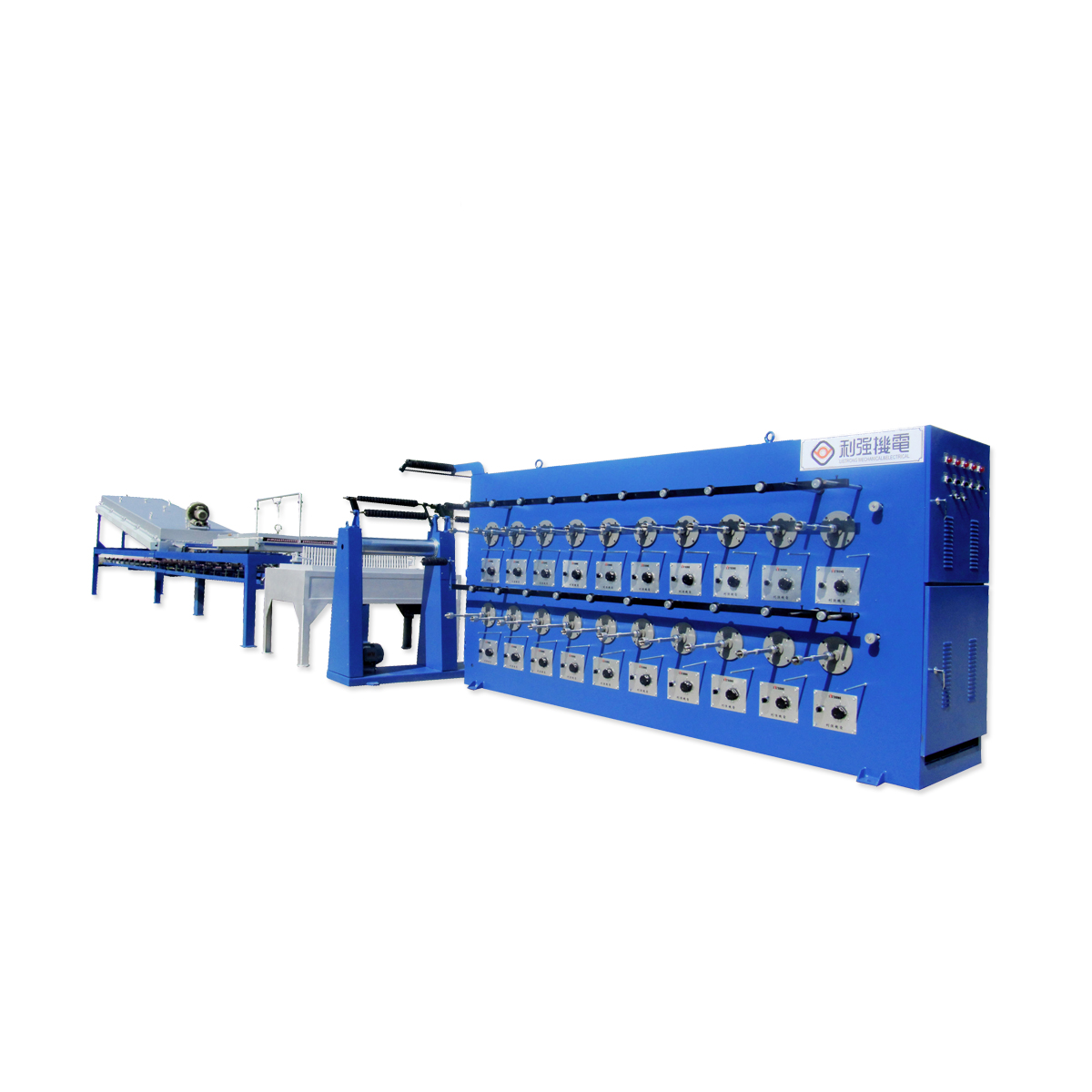
It's also worth noting how annealing improves downstream process efficiency. Softer wire post-annealing puts less strain on die systems in subsequent drawing stages, which translates into longer tool life and reduced operational costs. For end users, this means fewer defects, better coil shape, and less machine downtime. As a wire annealing machine manufacturer with years of industry insight, we’ve observed that investing in the right machine upfront pays off in both product consistency and overall production economy.
While the core science of wire annealing has been known for decades, the technology surrounding it has evolved considerably. Today’s systems feature precise feedback loops, PLC control, and real-time data logging, enabling smarter production and faster quality assurance. This evolution not only ensures tighter control over metallurgical outcomes but also aligns with the increasing need for process transparency and traceability in modern manufacturing environments.
In short, understanding how wire annealing influences metallurgical properties is key to selecting the right machine and configuring it for your unique production goals. A high-performance Wire Annealing Machine isn’t just a piece of equipment—it’s a strategic investment in the reliability, efficiency, and marketability of your wire products. Let our expertise help you build the foundation for long-term manufacturing success.
Contact Us