Modern wire production demands more than just mechanical reliability—it requires intelligent systems that adapt, respond, and maintain consistency in high-speed industrial environments. At the heart of the automatic wire take up machine is a network of advanced control systems that do much more than guide the wire. These systems play a critical role in ensuring smooth operation, precise winding, and real-time adaptability across different wire types and diameters. As production standards tighten and demand increases, automation technologies in take-up machines have become indispensable for manufacturers seeking both quality and efficiency.
The core of this automation is typically a PLC (Programmable Logic Controller), which acts as the brain of the machine. These industrial computers monitor sensor feedback, regulate motor speeds, and adjust tension dynamically to prevent wire deformation or breakage. By programming specific parameters for copper, aluminum, or steel wires, operators can minimize setup times and optimize for different production batches. For manufacturers running 24/7 operations, these intelligent systems provide the consistency and repeatability that manual or semi-automatic setups simply can’t match.
Closely integrated with the PLC are a variety of high-precision sensors and encoders that track rotation speed, coil tension, and alignment. These sensors feed continuous data back to the controller, enabling real-time corrections without interrupting production. For example, if the wire deviates slightly from its optimal coiling path, the system can make micro-adjustments instantly—preserving the quality of the coil and reducing waste. In advanced models of the automatic wire take-up machine, even ambient temperature and motor load are monitored to maintain system balance under various operational loads.
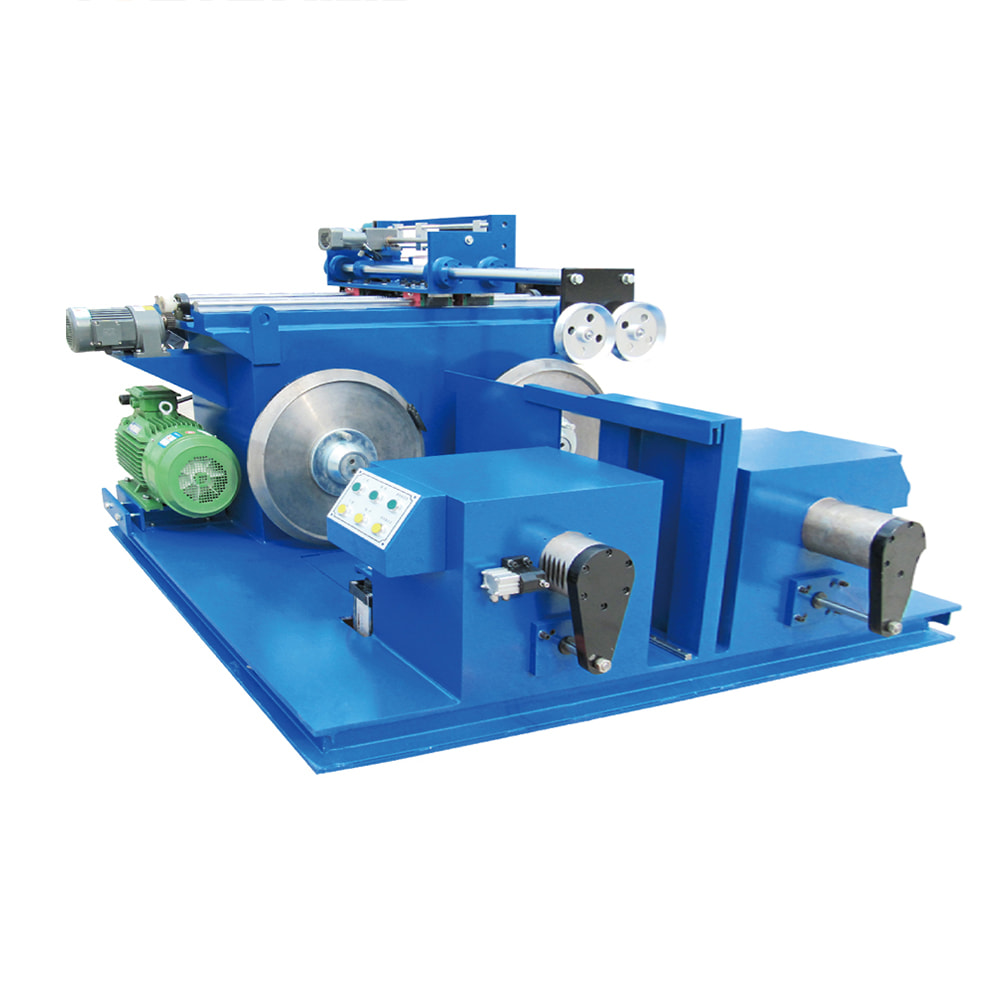
Motor control technology also plays a vital role in performance. Variable frequency drives (VFDs) are commonly used to fine-tune motor acceleration and deceleration, which is especially important when dealing with wires of different tensile strengths. Smooth motor control not only ensures even layering during coiling but also minimizes mechanical wear and tear on the equipment. This results in fewer unplanned downtimes and longer machine lifespan—something every production manager values when calculating return on investment.
What truly sets high-end wire take-up systems apart is their user interface and remote diagnostics capabilities. Intuitive touchscreens allow operators to switch wire programs, set coiling patterns, and review error logs with ease. Remote access features—available in many modern machines—mean that performance data can be monitored and even adjusted from a central control room or off-site location. This level of control helps large operations maintain centralized oversight of multiple production lines without compromising on accuracy or responsiveness.
Importantly, the use of imported electrical components in quality wire take-up machines ensures not only stability but also global compatibility. Components from trusted brands come with extensive certifications and better long-term availability for replacement, which is crucial for export-focused factories or those operating under international compliance standards. This attention to component quality contributes to the overall reliability of the system, reinforcing the machine’s role as a long-term asset rather than a temporary solution.
For manufacturers looking to scale production while reducing operator dependence, investing in a fully automated wire take-up machine with advanced control systems is a future-proof move. It’s not just about automation—it’s about building a smarter, more responsive production line that supports consistent quality with minimal supervision. Whether you're handling large-scale copper wire output or shifting between wire grades, a thoughtfully engineered system brings peace of mind and sustained productivity, backed by proven industrial technology.
Contact Us